ਫੀਡ ਪੈਲੇਟ ਮਸ਼ੀਨ ਦੀ ਦਾਣੇਦਾਰ ਪ੍ਰਕਿਰਿਆ ਦੌਰਾਨ, ਵੱਖ-ਵੱਖ ਰੰਗਾਂ ਵਾਲੇ ਵਿਅਕਤੀਗਤ ਫੀਡ ਪੈਲੇਟ ਜਾਂ ਵਿਅਕਤੀਗਤ ਫੀਡ ਪੈਲੇਟ ਹੁੰਦੇ ਹਨ, ਜਿਨ੍ਹਾਂ ਨੂੰ ਆਮ ਤੌਰ 'ਤੇ "ਫੁੱਲ ਫੀਡ" ਕਿਹਾ ਜਾਂਦਾ ਹੈ। ਇਹ ਸਥਿਤੀ ਜਲ-ਫੀਡ ਦੇ ਉਤਪਾਦਨ ਵਿੱਚ ਆਮ ਹੈ, ਮੁੱਖ ਤੌਰ 'ਤੇ ਰਿੰਗ ਡਾਈ ਤੋਂ ਕੱਢੇ ਗਏ ਵਿਅਕਤੀਗਤ ਕਣਾਂ ਦਾ ਰੰਗ ਦੂਜੇ ਆਮ ਕਣਾਂ ਨਾਲੋਂ ਗੂੜ੍ਹਾ ਜਾਂ ਹਲਕਾ ਹੋਣ, ਜਾਂ ਵਿਅਕਤੀਗਤ ਕਣਾਂ ਦੀ ਸਤ੍ਹਾ ਦਾ ਰੰਗ ਅਸੰਗਤ ਹੋਣ ਦੇ ਰੂਪ ਵਿੱਚ ਪ੍ਰਗਟ ਹੁੰਦਾ ਹੈ, ਜਿਸ ਨਾਲ ਫੀਡ ਦੇ ਪੂਰੇ ਬੈਚ ਦੀ ਦਿੱਖ ਗੁਣਵੱਤਾ ਪ੍ਰਭਾਵਿਤ ਹੁੰਦੀ ਹੈ।
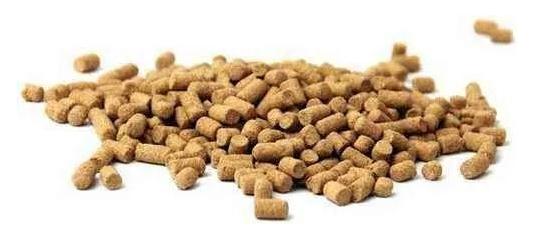
ਇਸ ਵਰਤਾਰੇ ਦੇ ਮੁੱਖ ਕਾਰਨ ਹੇਠ ਲਿਖੇ ਅਨੁਸਾਰ ਹਨ:
a)ਫੀਡ ਕੱਚੇ ਮਾਲ ਦੀ ਬਣਤਰ ਬਹੁਤ ਗੁੰਝਲਦਾਰ ਹੈ, ਬਹੁਤ ਸਾਰੀਆਂ ਕਿਸਮਾਂ ਦੇ ਕੱਚੇ ਮਾਲ, ਅਸਮਾਨ ਮਿਸ਼ਰਣ, ਅਤੇ ਫੀਡ ਕਣਾਂ ਨੂੰ ਪ੍ਰੋਸੈਸ ਕਰਨ ਤੋਂ ਪਹਿਲਾਂ ਪਾਊਡਰ ਦੀ ਅਸੰਗਤ ਨਮੀ ਦੇ ਨਾਲ।
b)ਦਾਣੇ ਬਣਾਉਣ ਲਈ ਵਰਤੇ ਜਾਣ ਵਾਲੇ ਕੱਚੇ ਮਾਲ ਦੀ ਨਮੀ ਦੀ ਮਾਤਰਾ ਅਸੰਗਤ ਹੁੰਦੀ ਹੈ। ਜਲ-ਭੋਜਨ ਦੀ ਉਤਪਾਦਨ ਪ੍ਰਕਿਰਿਆ ਵਿੱਚ, ਅਲਟਰਾਫਾਈਨ ਕੁਚਲਣ ਤੋਂ ਬਾਅਦ ਕੱਚੇ ਮਾਲ ਵਿੱਚ ਪਾਣੀ ਦੇ ਨੁਕਸਾਨ ਦੀ ਭਰਪਾਈ ਕਰਨ ਲਈ ਅਕਸਰ ਮਿਕਸਰ ਵਿੱਚ ਥੋੜ੍ਹੀ ਜਿਹੀ ਮਾਤਰਾ ਵਿੱਚ ਪਾਣੀ ਪਾਉਣਾ ਜ਼ਰੂਰੀ ਹੁੰਦਾ ਹੈ। ਮਿਲਾਉਣ ਤੋਂ ਬਾਅਦ, ਇਸਨੂੰ ਫਿਰ ਟੈਂਪਰਿੰਗ ਲਈ ਕੰਡੀਸ਼ਨਰ ਵਿੱਚ ਭੇਜਿਆ ਜਾਂਦਾ ਹੈ। ਕੁਝ ਫੀਡ ਨਿਰਮਾਤਾ ਫੀਡ ਬਣਾਉਣ ਲਈ ਇੱਕ ਬਹੁਤ ਜ਼ਿਆਦਾ ਸਧਾਰਨ ਪ੍ਰਕਿਰਿਆ ਦੀ ਵਰਤੋਂ ਕਰਦੇ ਹਨ - ਫਾਰਮੂਲੇ ਲਈ ਲੋੜੀਂਦੀ ਸਮੱਗਰੀ ਨੂੰ ਸਿੱਧੇ ਮਿਕਸਰ ਵਿੱਚ ਪਾਓ ਅਤੇ ਕਾਫ਼ੀ ਪਾਣੀ ਪਾਓ, ਪੇਸ਼ੇਵਰ ਜ਼ਰੂਰਤਾਂ ਦੇ ਅਨੁਸਾਰ ਇੱਕ ਵਿਸਤ੍ਰਿਤ ਅਤੇ ਹੌਲੀ ਜੋੜਨ ਦੀ ਪ੍ਰਕਿਰਿਆ ਨੂੰ ਪੂਰਾ ਕਰਨ ਦੀ ਬਜਾਏ। ਇਸ ਲਈ, ਉਹਨਾਂ ਨੂੰ ਪਾਣੀ ਦੀ ਘੁਲਣਸ਼ੀਲਤਾ ਦੇ ਮਾਮਲੇ ਵਿੱਚ ਫੀਡ ਸਮੱਗਰੀ ਦੀ ਸੰਤੁਲਿਤ ਵੰਡ ਨੂੰ ਯਕੀਨੀ ਬਣਾਉਣਾ ਮੁਸ਼ਕਲ ਲੱਗਦਾ ਹੈ। ਜਦੋਂ ਅਸੀਂ ਕੰਡੀਸ਼ਨਿੰਗ ਇਲਾਜ ਲਈ ਇਹਨਾਂ ਮਿਸ਼ਰਤ ਸਮੱਗਰੀਆਂ ਦੀ ਵਰਤੋਂ ਕਰਦੇ ਹਾਂ, ਤਾਂ ਅਸੀਂ ਪਾਵਾਂਗੇ ਕਿ ਕੰਡੀਸ਼ਨਰ ਦੀ ਕੁਸ਼ਲਤਾ ਦੇ ਕਾਰਨ, ਨਮੀ ਦੀ ਮਾਤਰਾ ਨੂੰ ਤੇਜ਼ੀ ਨਾਲ ਬਰਾਬਰ ਨਹੀਂ ਖਿੰਡਾਇਆ ਜਾ ਸਕਦਾ। ਇਸ ਲਈ, ਭਾਫ਼ ਕਿਰਿਆ ਅਧੀਨ ਪ੍ਰੋਸੈਸ ਕੀਤੇ ਫੀਡ ਉਤਪਾਦਾਂ ਦੀ ਪਰਿਪੱਕਤਾ ਵੱਖ-ਵੱਖ ਹਿੱਸਿਆਂ ਵਿੱਚ ਬਹੁਤ ਵੱਖਰੀ ਹੁੰਦੀ ਹੈ, ਅਤੇ ਦਾਣੇ ਬਣਾਉਣ ਤੋਂ ਬਾਅਦ ਰੰਗ ਲੜੀ ਕਾਫ਼ੀ ਸਪੱਸ਼ਟ ਨਹੀਂ ਹੁੰਦੀ ਹੈ।
c)ਗ੍ਰੇਨੂਲੇਸ਼ਨ ਬਿਨ ਵਿੱਚ ਵਾਰ-ਵਾਰ ਗ੍ਰੇਨੂਲੇਸ਼ਨ ਵਾਲੀਆਂ ਰੀਸਾਈਕਲ ਕੀਤੀਆਂ ਸਮੱਗਰੀਆਂ ਹਨ। ਗ੍ਰੇਨੂਲੇਸ਼ਨ ਤੋਂ ਬਾਅਦ ਗ੍ਰੇਨੂਲੇਸ਼ਨ ਵਾਲੀ ਸਮੱਗਰੀ ਨੂੰ ਠੰਡਾ ਅਤੇ ਸਕ੍ਰੀਨ ਕੀਤੇ ਜਾਣ ਤੋਂ ਬਾਅਦ ਹੀ ਤਿਆਰ ਉਤਪਾਦ ਵਿੱਚ ਬਦਲਿਆ ਜਾ ਸਕਦਾ ਹੈ। ਸਕ੍ਰੀਨ ਕੀਤਾ ਗਿਆ ਬਾਰੀਕ ਪਾਊਡਰ ਜਾਂ ਛੋਟੇ ਕਣਾਂ ਵਾਲੀ ਸਮੱਗਰੀ ਅਕਸਰ ਰੀਗ੍ਰੇਨੂਲੇਸ਼ਨ ਲਈ ਉਤਪਾਦਨ ਪ੍ਰਕਿਰਿਆ ਵਿੱਚ ਦਾਖਲ ਹੁੰਦੀ ਹੈ, ਆਮ ਤੌਰ 'ਤੇ ਮਿਕਸਰ ਵਿੱਚ ਜਾਂ ਗ੍ਰੇਨੂਲੇਸ਼ਨ ਸਾਈਲੋ ਦੀ ਉਡੀਕ ਵਿੱਚ। ਇਸ ਤੱਥ ਦੇ ਕਾਰਨ ਕਿ ਇਸ ਕਿਸਮ ਦੀ ਵਾਪਸੀ ਸਮੱਗਰੀ ਨੂੰ ਦੁਬਾਰਾ ਕੰਡੀਸ਼ਨ ਕੀਤਾ ਜਾਂਦਾ ਹੈ ਅਤੇ ਦਾਣੇਦਾਰ ਬਣਾਇਆ ਜਾਂਦਾ ਹੈ, ਜੇਕਰ ਇਸਨੂੰ ਹੋਰ ਸਹਾਇਕ ਸਮੱਗਰੀਆਂ ਨਾਲ ਅਸਮਾਨ ਢੰਗ ਨਾਲ ਮਿਲਾਇਆ ਜਾਂਦਾ ਹੈ ਜਾਂ ਕੰਡੀਸ਼ਨਿੰਗ ਤੋਂ ਬਾਅਦ ਰਿਟਰਨ ਮਸ਼ੀਨ ਛੋਟੇ ਕਣ ਸਮੱਗਰੀਆਂ ਨਾਲ ਮਿਲਾਇਆ ਜਾਂਦਾ ਹੈ, ਤਾਂ ਇਹ ਕਈ ਵਾਰ ਕੁਝ ਫੀਡ ਫਾਰਮੂਲਿਆਂ ਲਈ "ਫੁੱਲ ਸਮੱਗਰੀ" ਪੈਦਾ ਕਰ ਸਕਦਾ ਹੈ।
d)ਰਿੰਗ ਡਾਈ ਅਪਰਚਰ ਦੀ ਅੰਦਰੂਨੀ ਕੰਧ ਦੀ ਨਿਰਵਿਘਨਤਾ ਅਸੰਗਤ ਹੈ। ਡਾਈ ਹੋਲ ਦੀ ਅਸੰਗਤ ਸਤਹ ਫਿਨਿਸ਼ ਦੇ ਕਾਰਨ, ਐਕਸਟਰੂਜ਼ਨ ਦੌਰਾਨ ਵਸਤੂ ਦਾ ਅਨੁਭਵ ਹੋਣ ਵਾਲਾ ਵਿਰੋਧ ਅਤੇ ਐਕਸਟਰੂਜ਼ਨ ਦਬਾਅ ਵੱਖਰਾ ਹੁੰਦਾ ਹੈ, ਜਿਸਦੇ ਨਤੀਜੇ ਵਜੋਂ ਰੰਗ ਵਿੱਚ ਅਸੰਗਤ ਤਬਦੀਲੀਆਂ ਆਉਂਦੀਆਂ ਹਨ। ਇਸ ਤੋਂ ਇਲਾਵਾ, ਕੁਝ ਰਿੰਗ ਡਾਈਸ ਵਿੱਚ ਛੋਟੇ ਛੇਕ ਵਾਲੀਆਂ ਕੰਧਾਂ 'ਤੇ ਬਰਰ ਹੁੰਦੇ ਹਨ, ਜੋ ਐਕਸਟਰੂਜ਼ਨ ਦੌਰਾਨ ਕਣਾਂ ਦੀ ਸਤ੍ਹਾ ਨੂੰ ਖੁਰਚ ਸਕਦੇ ਹਨ, ਨਤੀਜੇ ਵਜੋਂ ਵਿਅਕਤੀਗਤ ਕਣਾਂ ਲਈ ਵੱਖ-ਵੱਖ ਸਤਹ ਰੰਗ ਹੁੰਦੇ ਹਨ।
ਉੱਪਰ ਸੂਚੀਬੱਧ "ਫੁੱਲ ਸਮੱਗਰੀ" ਪੈਦਾ ਕਰਨ ਦੇ ਚਾਰ ਕਾਰਨਾਂ ਲਈ ਸੁਧਾਰ ਦੇ ਤਰੀਕੇ ਪਹਿਲਾਂ ਹੀ ਬਹੁਤ ਸਪੱਸ਼ਟ ਹਨ, ਮੁੱਖ ਤੌਰ 'ਤੇ ਫਾਰਮੂਲੇ ਵਿੱਚ ਹਰੇਕ ਹਿੱਸੇ ਦੀ ਮਿਸ਼ਰਣ ਇਕਸਾਰਤਾ ਅਤੇ ਸ਼ਾਮਲ ਕੀਤੇ ਗਏ ਪਾਣੀ ਦੀ ਮਿਸ਼ਰਣ ਇਕਸਾਰਤਾ ਨੂੰ ਨਿਯੰਤਰਿਤ ਕਰਨਾ; ਬੁਝਾਉਣ ਅਤੇ ਟੈਂਪਰਿੰਗ ਪ੍ਰਦਰਸ਼ਨ ਨੂੰ ਬਿਹਤਰ ਬਣਾਉਣ ਨਾਲ ਰੰਗ ਤਬਦੀਲੀਆਂ ਘੱਟ ਸਕਦੀਆਂ ਹਨ; ਵਾਪਸੀ ਮਸ਼ੀਨ ਸਮੱਗਰੀ ਨੂੰ ਨਿਯੰਤਰਿਤ ਕਰੋ। ਉਹਨਾਂ ਫਾਰਮੂਲਿਆਂ ਲਈ ਜੋ "ਫੁੱਲ ਸਮੱਗਰੀ" ਪੈਦਾ ਕਰਨ ਦੀ ਸੰਭਾਵਨਾ ਰੱਖਦੇ ਹਨ, ਵਾਪਸੀ ਮਸ਼ੀਨ ਸਮੱਗਰੀ ਨੂੰ ਸਿੱਧੇ ਤੌਰ 'ਤੇ ਦਾਣੇਦਾਰ ਨਾ ਬਣਾਉਣ ਦੀ ਕੋਸ਼ਿਸ਼ ਕਰੋ। ਵਾਪਸੀ ਮਸ਼ੀਨ ਸਮੱਗਰੀ ਨੂੰ ਕੱਚੇ ਮਾਲ ਨਾਲ ਮਿਲਾਇਆ ਜਾਣਾ ਚਾਹੀਦਾ ਹੈ ਅਤੇ ਦੁਬਾਰਾ ਕੁਚਲਿਆ ਜਾਣਾ ਚਾਹੀਦਾ ਹੈ; ਡਾਈ ਹੋਲਜ਼ ਦੀ ਨਿਰਵਿਘਨਤਾ ਨੂੰ ਨਿਯੰਤਰਿਤ ਕਰਨ ਲਈ ਉੱਚ-ਗੁਣਵੱਤਾ ਵਾਲੇ ਰਿੰਗ ਡਾਈ ਹੋਲਜ਼ ਦੀ ਵਰਤੋਂ ਕਰੋ, ਅਤੇ ਜੇ ਜ਼ਰੂਰੀ ਹੋਵੇ, ਤਾਂ ਵਰਤੋਂ ਤੋਂ ਪਹਿਲਾਂ ਰਿੰਗ ਡਾਈ ਹੋਲਜ਼ ਨੂੰ ਪੀਸੋ।
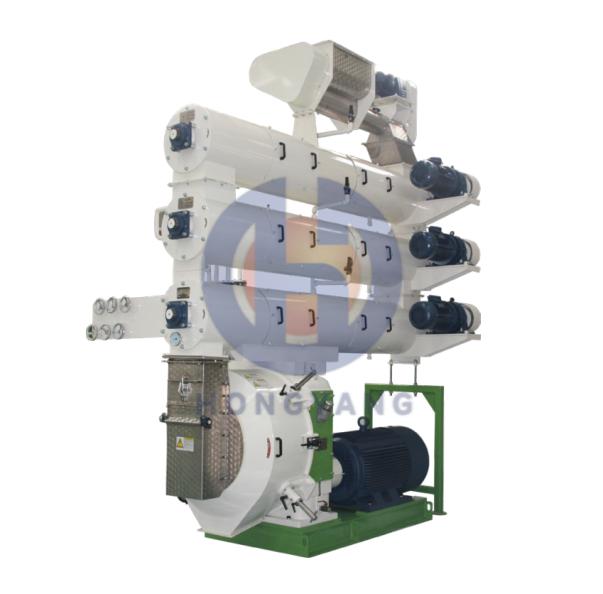
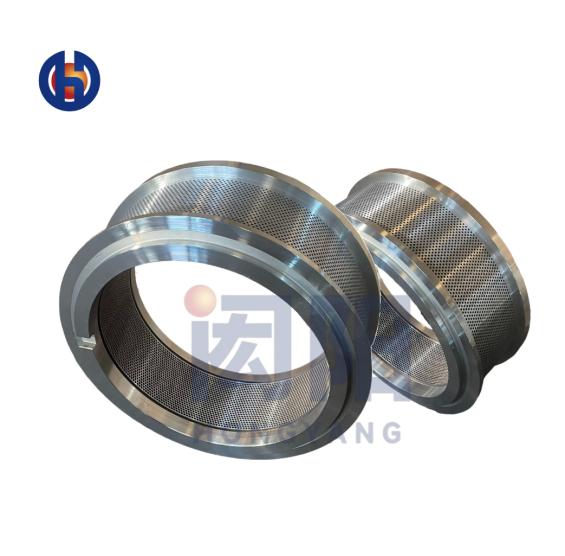
ਦੋ-ਪਰਤ ਦੋਹਰੇ ਧੁਰੇ ਵਾਲੇ ਡਿਫਰੈਂਸ਼ੀਅਲ ਕੰਡੀਸ਼ਨਰ ਅਤੇ ਦੋ-ਪਰਤ ਵਾਲੇ ਐਕਸਟੈਂਡਡ ਜੈਕੇਟ ਕੰਡੀਸ਼ਨਰ ਨੂੰ ਕੌਂਫਿਗਰ ਕਰਨ ਦੀ ਸਿਫਾਰਸ਼ ਕੀਤੀ ਜਾਂਦੀ ਹੈ, ਜਿਸਦਾ ਬੁਝਾਉਣ ਦਾ ਸਮਾਂ 60-120 ਸਕਿੰਟਾਂ ਤੱਕ ਹੁੰਦਾ ਹੈ ਅਤੇ 100 ℃ ਤੋਂ ਵੱਧ ਤਾਪਮਾਨ ਹੁੰਦਾ ਹੈ। ਬੁਝਾਉਣ ਦੀ ਪ੍ਰਕਿਰਿਆ ਇਕਸਾਰ ਹੁੰਦੀ ਹੈ ਅਤੇ ਪ੍ਰਦਰਸ਼ਨ ਸ਼ਾਨਦਾਰ ਹੁੰਦਾ ਹੈ। ਮਲਟੀ-ਪੁਆਇੰਟ ਏਅਰ ਇਨਟੇਕ ਦੀ ਵਰਤੋਂ ਸਮੱਗਰੀ ਅਤੇ ਭਾਫ਼ ਦੇ ਕਰਾਸ-ਸੈਕਸ਼ਨਲ ਖੇਤਰ ਨੂੰ ਬਹੁਤ ਵਧਾਉਂਦੀ ਹੈ, ਜਿਸ ਨਾਲ ਸਮੱਗਰੀ ਦੀ ਪਰਿਪੱਕਤਾ ਵਿੱਚ ਸੁਧਾਰ ਹੁੰਦਾ ਹੈ ਅਤੇ ਬੁਝਾਉਣ ਅਤੇ ਟੈਂਪਰਿੰਗ ਪ੍ਰਭਾਵ ਵਿੱਚ ਸੁਧਾਰ ਹੁੰਦਾ ਹੈ; ਡਿਜੀਟਲ ਇੰਸਟ੍ਰੂਮੈਂਟ ਪੈਨਲ ਅਤੇ ਤਾਪਮਾਨ ਸੈਂਸਰ ਕੰਡੀਸ਼ਨਿੰਗ ਦੇ ਤਾਪਮਾਨ ਨੂੰ ਪ੍ਰਦਰਸ਼ਿਤ ਕਰ ਸਕਦੇ ਹਨ, ਜਿਸ ਨਾਲ ਉਪਭੋਗਤਾਵਾਂ ਲਈ ਕਿਸੇ ਵੀ ਸਮੇਂ ਨਿਯੰਤਰਣ ਕਰਨਾ ਆਸਾਨ ਹੋ ਜਾਂਦਾ ਹੈ।
ਤਕਨੀਕੀ ਸਹਾਇਤਾ ਸੰਪਰਕ ਜਾਣਕਾਰੀ:
ਵਟਸਐਪ: +8618912316448
ਈ-ਮੇਲ:hongyangringdie@outlook.com
ਪੋਸਟ ਸਮਾਂ: ਜੁਲਾਈ-26-2023